STORY OF OUR MANUFACTURING
From scratch, we design, mold, produce, assemble, package and ship our each product in house. Throughout the process, we manage each step with immense precision & accuracy in the most efficient & sustainable manner.

1
RESEARCH & DEVELOPMENT
Our R&D is focused on creating unique and innovative products that set us apart from our competitors. Our commitment to discovering new and better ways to engineer high-quality products benefits our customers by enabling greater efficiency and profitability. Through high-end engineering, we design innovative products that either cost less or incorporate more advanced technology than our competitors, ensuring customer satisfaction.

2
ENGINEERING
Our engineers utilize cutting-edge technologies (CAD-CAM- AE, Unigraphics, Work NC, CadMold, Moldex, Lucidshape, Optis, SPEOS, etc.) to design components, products, and molds according to customer requirements. With over 50 years of experience, we deliver the fastest and most innovative solutions for all projects.

3
PROTOTYPING
At SERKO, we prioritize quality and precision in all aspects of our engineering work. That's why we create our prototypes in-house using the latest technology. This allows us to thoroughly test and analyze our products before they go into production, ensuring that they meet our high standards and the specific needs of our customers.

4
MOLD MAKING
Our mold-making department comprises highly skilled engineers and technicians who use the latest technology and extensive experience to meet precise customer mold requirements. Advanced quality and SPC techniques ensure precise mold production, expedited production, increased mold lifetime, and enhanced precision.

5
INJECTION MOLDING
Utilizing the latest machinery and our 50 years of plastic injection molding expertise, we produce plastic components in the most technological and efficient manner. Digitalization not only makes the production process more sustainable but also reduces the error rate, ensuring high-quality output. Our molding department uses fully electric, hybrid CNC molding machines to achieve precise and technical molding parts. Engineers and technicians employ advanced quality and SPC techniques to maintain control over process parameters, ensuring high product quality.
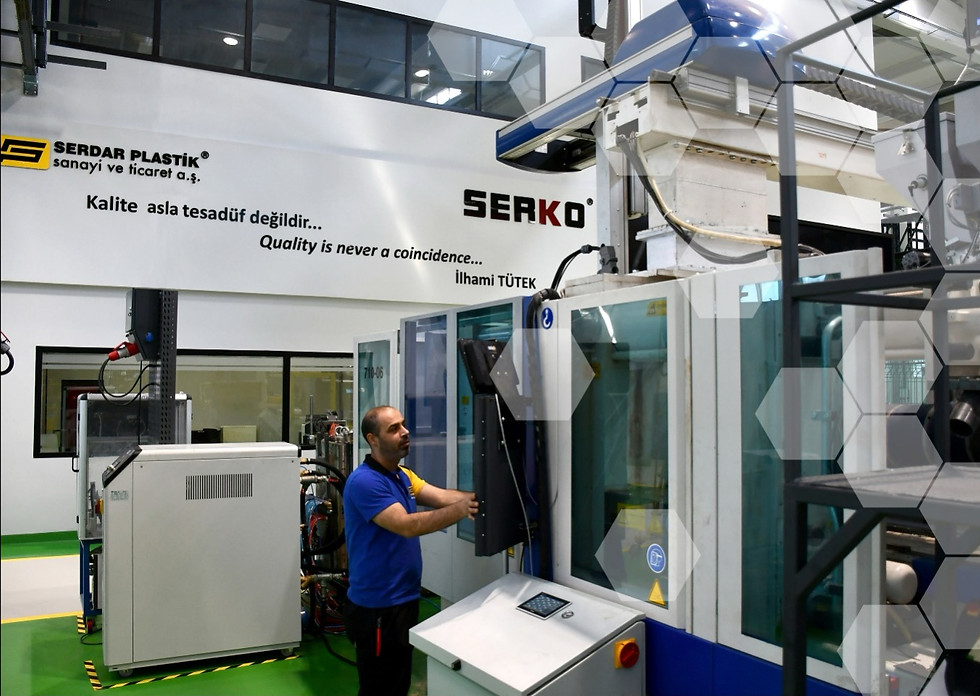
6
DECORATING
At SERKO, we use the latest technology and advanced methods to decorate our products efficiently and effectively. Our skilled engineering team specializes in through plating and hot stamping, ensuring that our products are both aesthetically pleasing and functional. We are committed to delivering excellence in everything we do, and our dedication to quality is evident in every project we undertake.

7
ASSEMBLY
After molding operations, components and products undergo assembly, coating, and testing with special apparatus and production lines. Post operations include hot stamping, UW welding, hot plate, tampography printing, silk printing, PVD vacuum metallization, PC hard coating, laser etching, plasma etching, punch press, riveting apparatus, and special production lines.

8
TESTING
Our hydraulic, optic, mechanic, and electronic laboratories within our R&D section allow us to test our products with precision. This enables us to identify weaknesses and enhance our technical know-how in automotive, thermotechnic, and appliance components.
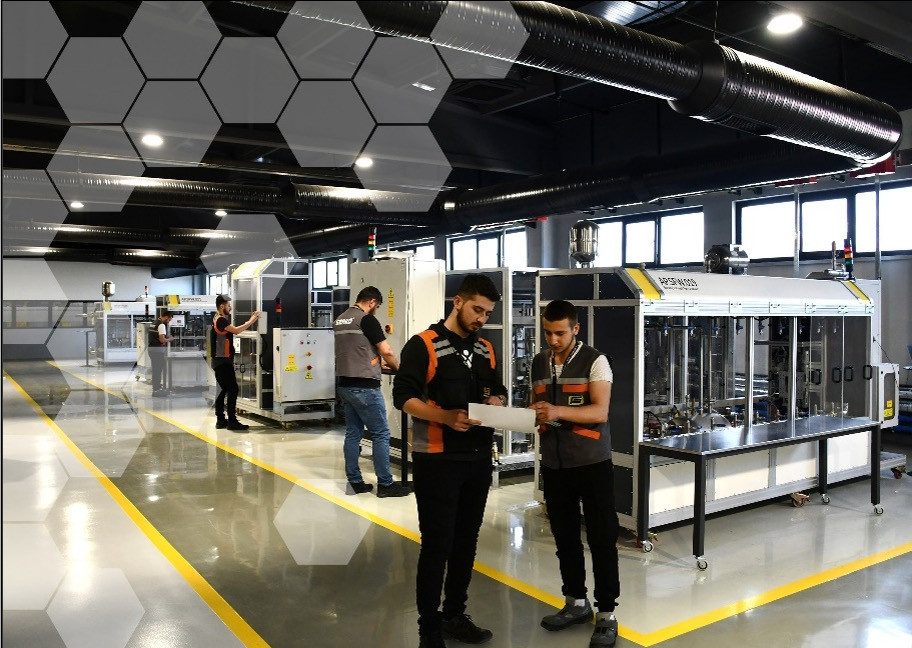
9
HOMOLOGATING
Our engineering products undergo a rigorous homologation process at SERKO, ensuring all our products are appropriately certified. We conduct in-house testing in our laboratories and further external tests to meet industry standards, including SAE/FMVSS and UNECE regulations. For thermotechnic components, we secure drinking water approvals and certifications such as WRAS and KTW, ensuring the highest quality for every product we ship.

10
LOGISTICS
Our logistics team manages raw materials and materials, integrating them into the automation system. They ensure the timely, proper quality, and accurate supply of required subcomponents and raw materials to production seat warehouses, performing milk run feedings at optimal times with lean production logic.
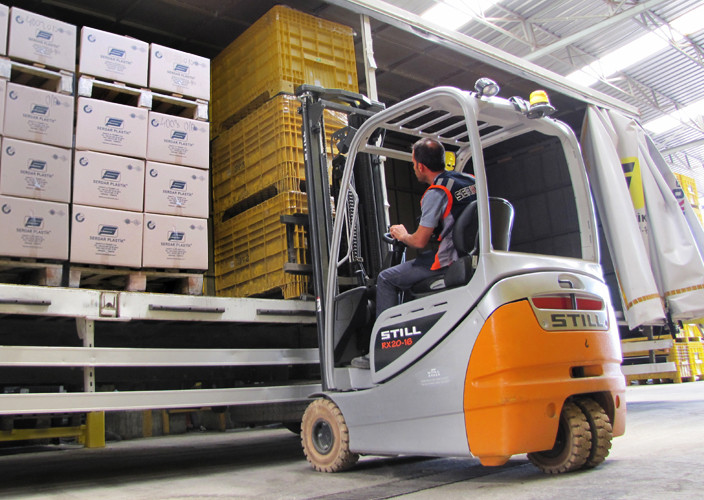